Auto parts machining technology inventory and summary - PTJ Manufacturing shop
Auto parts machining technology
A car is made up of many parts. Each part plays a different role. It needs to be processed by different processing methods before it can be installed on the car for use. What are the process of component processing? PTJ Manufacturing shop specializes in the processing of high-precision CNC machine tools. Its products are also involved in the field of auto parts. Today we have taken stock of the seven processes for auto parts processing. Let's take a look. |
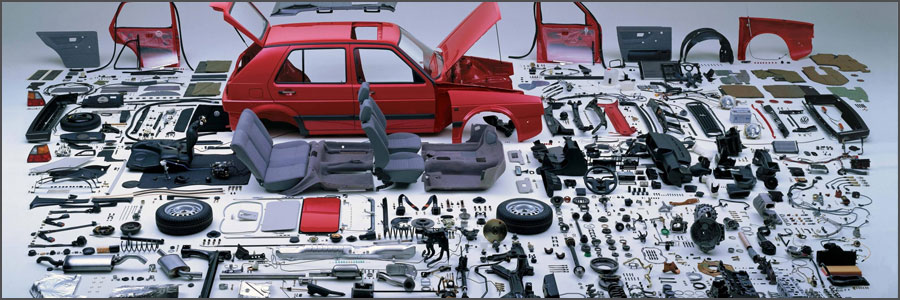
1、Auto parts forging machining
Forging processes are widely used in the automotive manufacturing process. Forging methods are divided into free forging and model forging. Free forging is a processing method in which a metal blank is placed on an anvil to withstand impact or pressure . The blanks of the car's gears and shafts are processed by free forging.
Model forging is a processing method in which a metal blank is placed in a die of a forging die and subjected to impact or pressure. Model forging is a bit like the process in which the dough is pressed into a biscuit shape in a mold. Compared with free forging, the shape of the workpiece produced by die forging is more complicated and the size is more precise. Typical examples of automotive forgings are: engine connecting rods and crankshafts, steering knuckles, automobile front axles, and the like.
2、Auto parts casting machining
Casting is a method of producing a product by pouring molten metal into a mold cavity and cooling and solidifying. In the process of manufacturing and manufacturing automotive parts, there are many parts made of cast iron, which account for about 10% of the total weight of the car, such as cylinder block, transmission case, steering gear housing, rear axle housing, brake drum, various Brackets, etc.
Cast iron parts are usually made of sand. The sand type raw material is mainly composed of sand and mixed with a binder, water, and the like. The sand material must have a certain bond strength in order to be molded into the desired shape and to withstand the scouring of high temperature molten iron without collapse. In order to mold a cavity in the sand mold that conforms to the shape of the casting, it is necessary to first make a model of wood, called a wood mold. The volume of the hot molten iron will be reduced after cooling. Therefore, the size of the wood mold needs to be increased according to the original size of the casting, and the surface to be machined is correspondingly thickened.
Hollow castings require the formation of a sand core and a corresponding core wood mold (core box). With a wooden mold, you can convert the cavity sand type (casting is also called "turning sand"). When manufacturing the sand mold, it is necessary to consider how the upper and lower sand boxes are separated to take out the wood mold, and also consider where the molten iron flows in, and how to fill the cavity to obtain a high quality casting. After the sand mold is made, it can be poured, that is, the molten iron is poured into the sand cavity. When pouring, the temperature of the molten iron is between 1250 and 1350 degrees, and the temperature is higher during melting.
3、Auto parts welding machining
Welding is a processing method in which two pieces of metal are locally heated or simultaneously heated and pressurized to be joined together. The welding method in which the common worker holds the mask in one hand and the welding tongs and the welding rod connected to the electric wire in the other hand is called manual arc welding, which is a high-temperature melting electrode and a weldment generated by arc discharge to be joined.
Manual arc welding is not widely used in automobile manufacturing. The most widely used in the manufacture of automobile bodies is spot welding. Spot welding is suitable for welding thin steel sheets. During operation, two electrodes are pressed against two steel sheets to bond them together, and the bonding points (circles with a diameter of 5-6 )) are heated and melted to be firmly joined. When two body parts are welded, the edges of the two parts are welded every 50-100 ,, so that the two parts form a discontinuous multi-point connection. Welding the entire car body usually requires thousands of solder joints. The strength of the solder joints is very high. Each solder joint can withstand a pulling force of 5kN, and even the steel sheet is torn, and the solder joint portion cannot be separated.
Gas welding, which is common in repair shops, is a method in which acetylene is burned and assisted by oxygen to generate a high-temperature flame to melt and join the electrode and the weldment. It is also possible to use this high temperature flame to cut the metal, called gas cutting. Gas welding and gas cutting applications are more flexible, but the heat affected zone of gas welding is larger, which causes deformation and metallographic structure changes of the weldment, and performance is degraded. Therefore, gas welding is rarely used in automobile manufacturing.
4、Cold stamping of automotive parts
Cold stamping or sheet stamping is a processing method in which a metal sheet is subjected to pressure in a die to be cut away or formed. Daily necessities, such as aluminum pans, lunch boxes, washbasins, etc., are made by cold stamping. For example, in the manufacture of a lunch box, it is first necessary to cut a rectangular shape and have four rounded blanks (referred to as "blackout" in the industry), and then press the blank into the female mold with a punch to form (known in the industry as "draw"). ). In the drawing process, the flat sheet becomes a box shape, the four sides of which are vertically bent upward, and the materials of the four corners are piled up and wrinkles are seen.
Automotive parts that are cold stamped are: engine oil sump, brake floor, car frame and most body parts. These parts are generally formed by blanking, punching, drawing, bending, flanging, trimming and the like. In order to manufacture cold stamped parts, a die must be prepared. The die is usually divided into two pieces, one of which is mounted on the press and can slide up and down, and the other is installed under the press and fixed. At the time of production, the blank is placed between two dies, and when the upper and lower dies are closed, the stamping process is completed. The productivity of stamping is high, and parts with complex shapes and high precision can be manufactured.
5、Auto parts cutting
Auto parts cutting is the process of cutting a metal blank layer by layer with a tool; the workpiece is obtained with the required shape, size and surface roughness. Metal cutting includes both fitter and machining. The fitter is a processing method for workers to cut with hand tools. It is flexible and convenient to operate, and is widely used in assembly and repair. Machining is done by means of machine tools, including: turning, planing, milling, drilling and grindin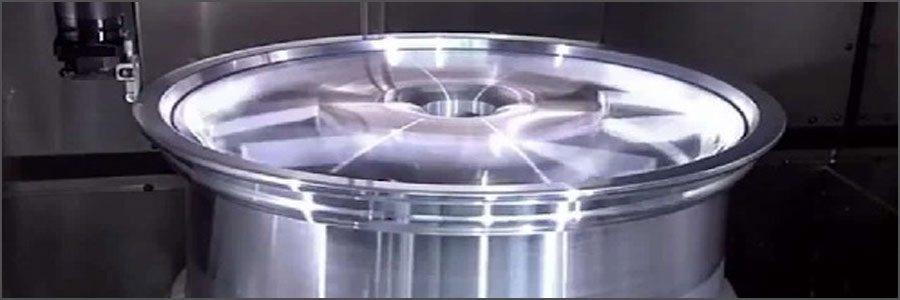
- Planing:It is the process of machining a workpiece with a planer. The planer is suitable for processing horizontal planes, vertical planes, slopes and grooves. The cylinder block and the cylinder head on the car, the matching plane of the transmission case and the cover are all processed by a planer.
- Turning:It is the process of machining a workpiece with a turning tool on a lathe. The lathe is suitable for cutting a variety of rotating surfaces, such as inner and outer cylinders or conical surfaces, as well as turning end faces. Many of the axle parts and gear blanks of the car are machined on a lathe.
- Milling:It is the process of machining a workpiece with a milling cutter on a milling machine. Milling machines can process bevels, grooves, and even old milling such as machined gears and curved surfaces for a wide range of automotive parts. The molds for cold stamping of automobile bodies are all milled. The computer-controlled CNC milling machine can process workpieces with complex shapes and is the main machine tool for modern machining.
- Grinding:It is the process of machining a workpiece with a grinding wheel on a grinding machine. Grinding is a finishing method that produces workpieces with high precision and roughness and that can grind workpieces with very high hardness. Some heat-treated automotive parts are finished with a grinding machine.
-
Drilling and boring are the main cutting methods for machining holes.
6、Heat treatment of automotive parts
Heat treatment is a method of reheating, holding or cooling solid steel to change its structure to meet the requirements of the parts or the process requirements. The temperature of the heating, the length of the holding time, and the speed of the cooling can cause different structural changes in the steel. The blacksmith immerses the heated steel in water and rapidly cools it (known as quenching by the expert), which increases the hardness of the steel, which is an example of heat treatment.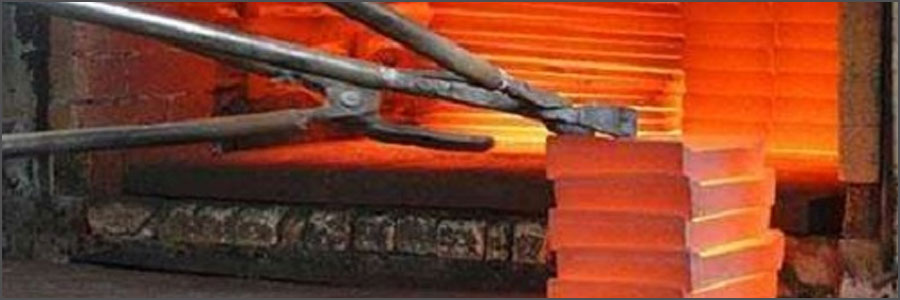
The heat treatment process includes annealing, normalizing, quenching, and tempering. Annealing is to heat the steel, heat it for a certain period of time, and then slowly cool it together with the furnace to obtain a finer and uniform structure and reduce the hardness to facilitate the cutting process. The normalizing heat is to heat the steel piece, take it out of the furnace after being kept warm, and then cool it in the air, which is suitable for refining the low carbon steel. Quenching is the heating of steel, which is quickly cooled in water or in oil to increase hardness. Tempering is usually a subsequent step of quenching. The quenched steel is reheated, cooled and then cooled to stabilize the structure and eliminate brittleness. There are many automotive parts, both to retain the toughness of the core, but also to change the surface structure to improve the hardness, it is necessary to use surface heat treatment such as high-frequency quenching or carburizing, cyanidation.
PTJ Machining Capabilities |
Automatic Bar Machining – Multi-spindle cam automatic screw machines CNC Turning – CNC delivers peak cost efficiency in shorter volumes, as well as high capacity production of mechanically simple components Custom Machining - with up to 12 axes of control Multi Spindle Machining- ISO 9001:2015 certified Screw Machine Products – The number of customized production parts per hour can reach 10000pcs Swiss Machining – with up to 9 axes of CNC control, to produce precision components with complex geometries in one operation High Volume Machining – 100 Advanced Production Turning Bar Automatics On-line and Ready CNC Milling - Machining Fully compliant with the exacting requirements of our customers 5 axis (11 axis) Machining – Tolerance | 0.1mm alignment |
What Can we help you do next?
∇ Get more information about cnc machining Shop
→Case study-Find out what we have done.
→Ralated tips about cnc machining services
By PTJ Manufacturing Shop|Categories: Blog|Tags: cnc milling services, cnc turning services, milling parts, turning parts, machining parts, special parts,faqs,technical news,company news,material news |Comments Off