Difference between turning and milling - PTJ Manufacturing Shop
Turning
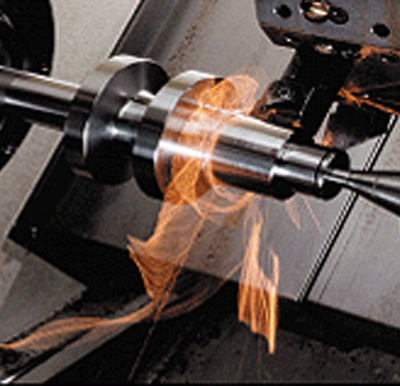
The process characteristics of turning
1. It is easy to ensure the positional accuracy of each working surface of the workpiecea. For example, it is easy to ensure coaxiality requirements
The workpiece is mounted by a chuck, and the axis of rotation is the axis of rotation of the lathe spindle
Using the front and rear top mounting workpieces, the axis of rotation is the center connection of the two top points
b. It is easy to ensure that the perpendicularity of the end face and the axis is required by the cross slide guide rail and the perpendicularity of the rotary axis of the workpiece
2. the cutting process is relatively stable to avoid the inertial force and impact force, allowing the use of larger cutting amount, high-speed cutting, which is conducive to productivity.
3. Suitable for finishing of non-ferrous metal parts
When the surface roughness of the non-ferrous metal parts is required to be small, the grinding value is not suitable, and turning or milling is required. When using a diamond turning tool for a fine car, it can achieve higher quality.
4. the tool is simple
Turning, sharpening and installation are convenient.
The application of turn
Different turning tools or other tools can be used on the lathe to process various turning surfaces, such as inner and outer cylindrical surfaces, inner and outer conical surfaces, threads, grooves, end faces and forming surfaces. The machining accuracy can reach IT8-IT7, surface roughness. The Ra value is 1.6 to 0.8, and turning is often used to machine parts with a single axis, such as straight shafts and general discs, sleeve parts, and the like. Multi-axis parts (such as crankshafts, eccentrics, etc.) or disc cams can also be machined if the position of the workpiece is changed or the lathe is properly modified. In the single-piece small batch production, various shafts, discs, sleeves and other parts are often processed with a wide-format horizontal lathe or CNC lathe; large parts with large diameter and short length (length to diameter ratio of 0.3 to 0.8) are used. Vertical lathe processing. In the case of a large number of small and medium-sized shafts and sleeves with inner holes and threads, the turret lathe should be used for processing. Large quantities and large quantities of small parts with less complicated shapes, such as screws, nuts and pipe joints. For the case of bushings, etc., semi-automatic and automatic lathes are often used for processing. It has high productivity but low precision.
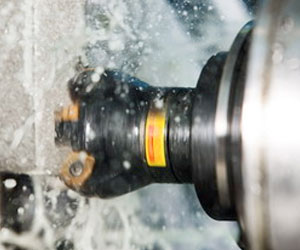
Milling refers to the cutting of metal parts with a rotatable circular multi-blade tool, which is one of the main methods of planar machining. It is often the rotation of the tool (the main motion), the workpiece is fixed (the workpiece can be fed with the movement of the table). Milling plane machines are available with horizontal or vertical lifting table milling machines for single-piece, small-volume production.
Milling end milling and peripheral milling. The end milling method uses a cutting edge on the end face of the milling cutter to mill the workpiece. The circumferential milling method uses a cutting edge on the circumferential surface of the milling cutter to mill the workpiece.
Milling characteristics
1. Each cutter of the milling cutter periodically participates in intermittent cutting
2. The cutting thickness of each tooth during the cutting process varies.
With the milling, the feed direction of the workpiece is the same as the direction of rotation of the milling cutter.
Up-cut milling, the direction of feed of the workpiece is opposite to the direction of rotation of the milling cutter.
In the actual production, the up-cut milling is often used, because the cutting force of the milling cutter will cause the workpiece to move forward under the condition of milling, the turbulence is due to the gap between the feed screw threads of the table, and the gap is in front of the movement, and the milling is smooth.
The cutting force is suddenly increased by the forward direction, causing the table and the workpiece to jump forward. But in fact, down-cut milling can reduce tool wear and improve surface finish. If you can eliminate the screw gap, it is better to follow the milling. However, there is no effective way to eliminate the gap. Therefore, the actual production is still used up-cut.
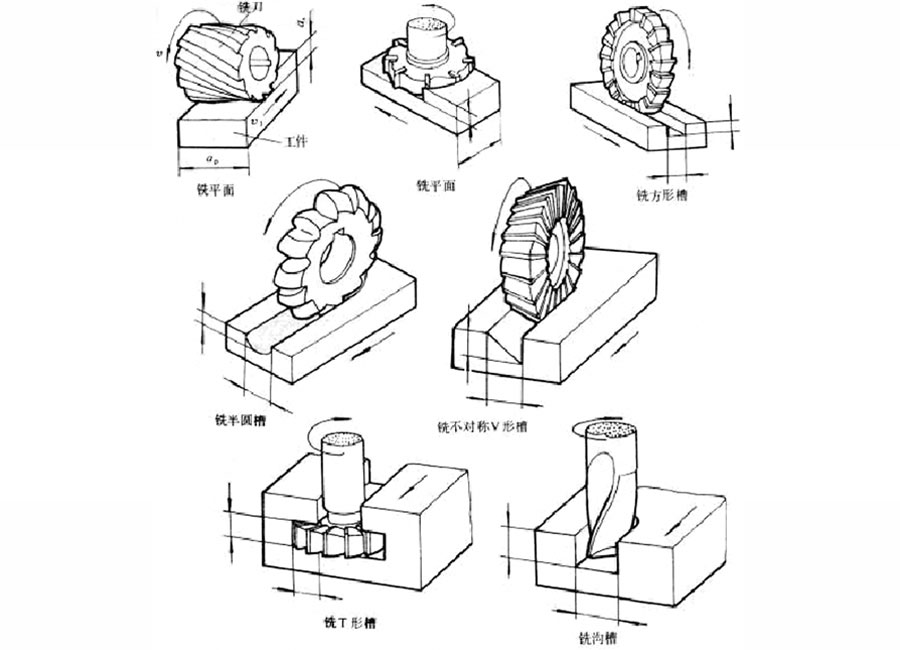
- the tool life is long when milling.
- the surface quality is good when milling.
- When clamping, the clamping force is smaller than that of up-cut milling.
- it is easy to cause the workpiece to move when going down.
PTJ Machining Capabilities |
Automatic Bar Machining – Multi-spindle cam automatic screw machines CNC Turning – CNC delivers peak cost efficiency in shorter volumes, as well as high capacity production of mechanically simple components Custom Machining - with up to 12 axes of control Multi Spindle Machining- ISO 9001:2015 certified Screw Machine Products – The number of customized production parts per hour can reach 10000pcs Swiss Machining – with up to 9 axes of CNC control, to produce precision components with complex geometries in one operation High Volume Machining – 100 Advanced Production Turning Bar Automatics On-line and Ready CNC Milling - Machining Fully compliant with the exacting requirements of our customers 5 axis (11 axis) Machining – Tolerance | 0.1mm alignment |
What Can we help you do next?
∇ Get more information about cnc machining Shop
→Case study-Find out what we have done.
→Ralated tips about cnc machining services
By PTJ Manufacturing Shop|Categories: Blog|Tags: cnc milling services, cnc turning services, milling parts, turning parts, machining parts, special parts,faqs,technical news,company news,material news |Comments Off